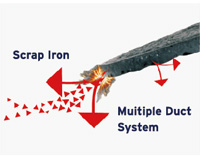
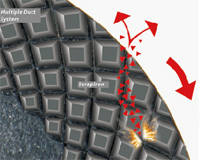
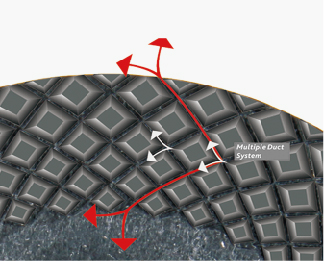

Flap disc has more advantages than grinding wheel, with the greater amount of grinding and the required gloss finish by different grits.
PEGATEC adopt the raw material from Germany, Turkey and so on. High quality abrasive particles and special structure can satisfy the rigorous and complex grinding operation for users.
Content | |
PEGATEC | High Performance |
PEGASTAR | Universality |
TERMINATOR |
|
Application types
Find the your products according to application and material
Material | Steel, Cast Steel | INOX | Rust, Cast Iron | Cast Iron, Stone |
Application | Page | Page | Page | Page |
Surface Grinding | 85 | 81-84 | 83 | — |
Welding Cleaning | 85 | 81-84 | 83 | — |
Chamfering | 85 | 81-84 | 83 | — |
De-burring | 85 | 81-84 | 83 | — |
Corner Welding | 85 | 81-84 | 83 | — |
TECHtips
Two Basic Flap Disc Designs
Type 29 Conical
THE MOST AGGRESSIVE CHOICE
- Conical flap discs have flaps angled at 10 degrees be used on both conical and flat surfaces and may
- The angle provides greater surface contact and as a result,tends to be the most aggressive choice
- The best choice when speed and stock removal are primary considerations
Type 27 Flat
THE CHOICE FOR THE BEST FINISH
- The Type 27 flap discs have a flat design and are used primarily on flat surfaces
- The best choice for smooth finishing
- Also available in Norton Jumbo / Merit High Density sizes with extra large flaps lasting up to 40% longer than standard flap discs
- Choice will alsCo depend on user preference of grinding angle (severe angle will weaken the edges)
Composition of coated abrasives:
Coated abrasives can be worked for almost all types material surface. Coated abrasives are divided into dry polishing and wetpolishing.
- Backing material
- Bottom glue
- Coating glue
- Grain
- Polishing lay
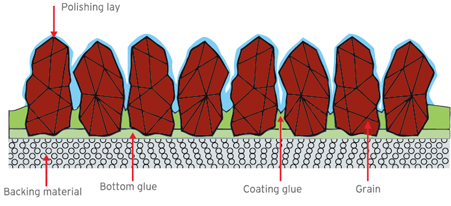
Backing material
Bonder and grain are fixed on backing material. The selection of backing material varies depending on tensile strength, flexibility, and wear-resisting. Backing material selection should take requirement of polishing into consideration. There are three kinds of PEGATEC as following:
Paper:
paper backing material are usually used for wood processing industry and paint processing, a small scale in metal processing. The abrasive products of manual polishing usually consist of 70-100g/M2 grain and paper backing material. Heavy paper is used for manufacturing narrow sanding belt and wide sanding belt for stationary machine.
Cloth:
cloth backing coated abrasives mainly used for metal processing industry.
Vulcanized fibre paper:
different intensity vulcanized fibre paper mainly for producing different fiber abrasives discs. Hard paper is very strong, hard, and wear-resisting.
Bond:
It needs different resin bond to combine abrasive grain with backing material in manufacturing coated abrasives. Firstly spray bottom glue on backing material, then spray abrasive grain on the surface, and take special technique to adjust. Then the abrasive grain and bond combine well. Bond supports abrasive grain well to bear external force and load in the processing.
Abrasives grain:
The right choice of products is very important for economic value of surface processing and technology.
Aluminium oxide:
Aluminum oxide is used for producing grain. It can change the hardness and toughness by bond and special manufacture method.
Silicon carbide:
silicon carbide is a kind of compositely produced abrasive grain. It is very sharp, low toughness, but with high hardness. Silicon material is used for titanium, aluminum, copper, stone and plastic working.
Zirconium:
zirconium is smelting mixture of aluminum oxide and zirconium oxide. Zirconium is softer but with more toughness compared with aluminum oxide. High proportion aluminum oxide endows zirconium excellent self-sharpness.
Ceramic grain:
The advanced grain toughness and self-sharpness are favored by various processing industry.
Classification of grain grit:
There are provisions of different coated abrasivegrain grit in ISO6344, and meanwhile apply to FEPA standard.
Previous | 1 | 2 | 3 | 4 | 5 | Next |